
Ballistics and impacts
Spinal cord trauma
A Fluid structure interaction analysis of spinal cord trauma
This analysis shows the results of a thesis research, which was also published in the Journal of Neurotrauma. [1]
The purpose of this analysis was to find the effect of cerebrospinal fluid (CSF) pressure and the existence of the epidural fat on the result of a spinal cord trauma caused by a burst fracture injury.
Both the CSF and the epidural fat modeled using the SPH numerical method for Lagrangian fluid modeling in an FSI simulation.
A new approach for a no-slip condition was also used which contribute to better momentum conservation in the in-compressible fluid being modeled as SPH.
The results shows that SPH can model both the fluid and the fat with pleasing accuracy, while conservation of momentum (pressure) is maintained when the proper particle seeding is used.
Also the research showed that higher CSF pressure can lead to higher strains on the spinal cord which can have neurological effects, and additionally, epidural fat has a considerable energy absorption capabilities which shouldn't be neglected in future studies.
Internal Ballistics
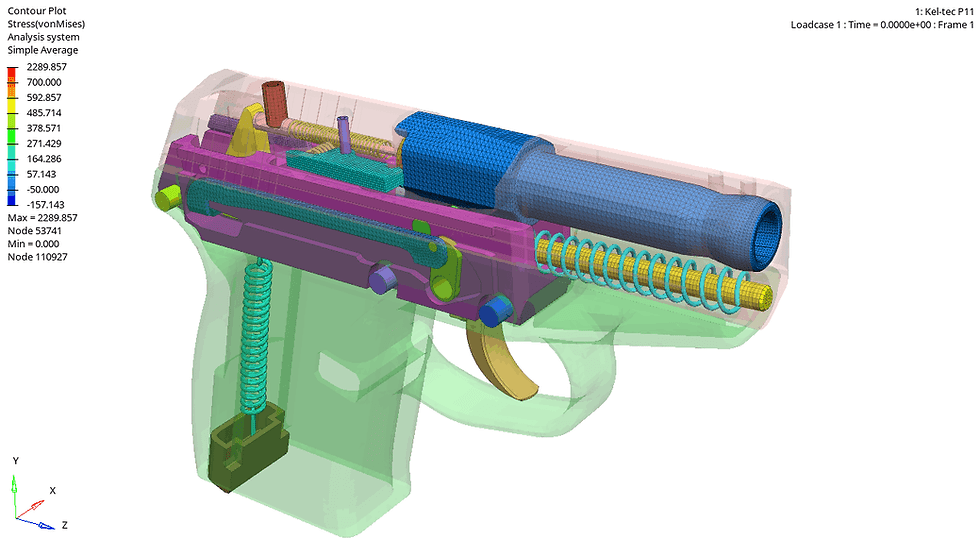
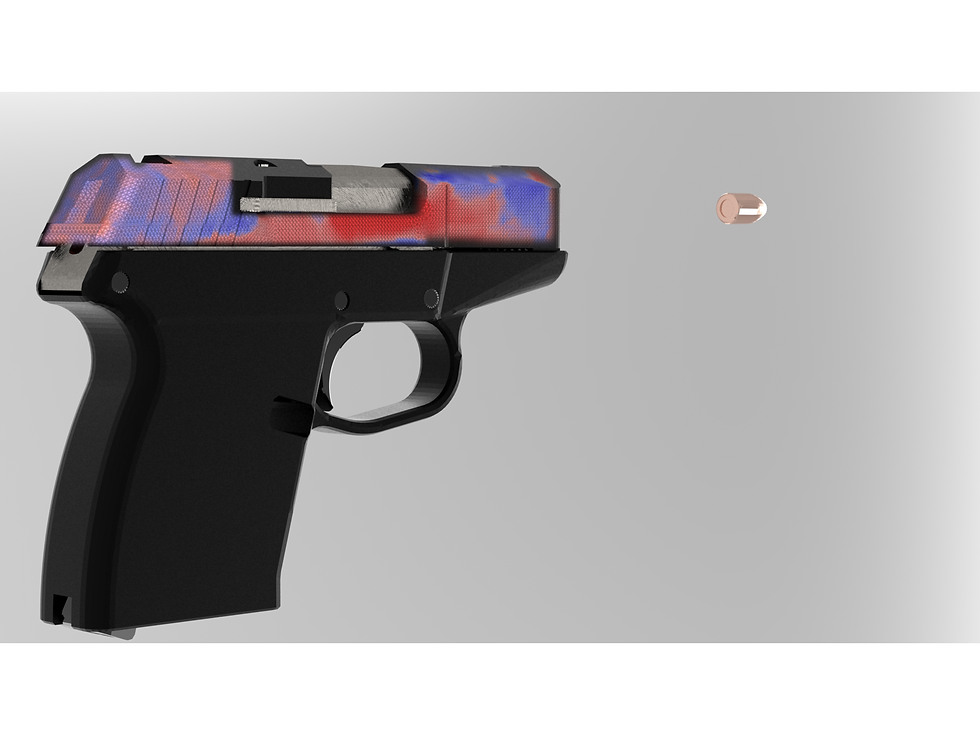
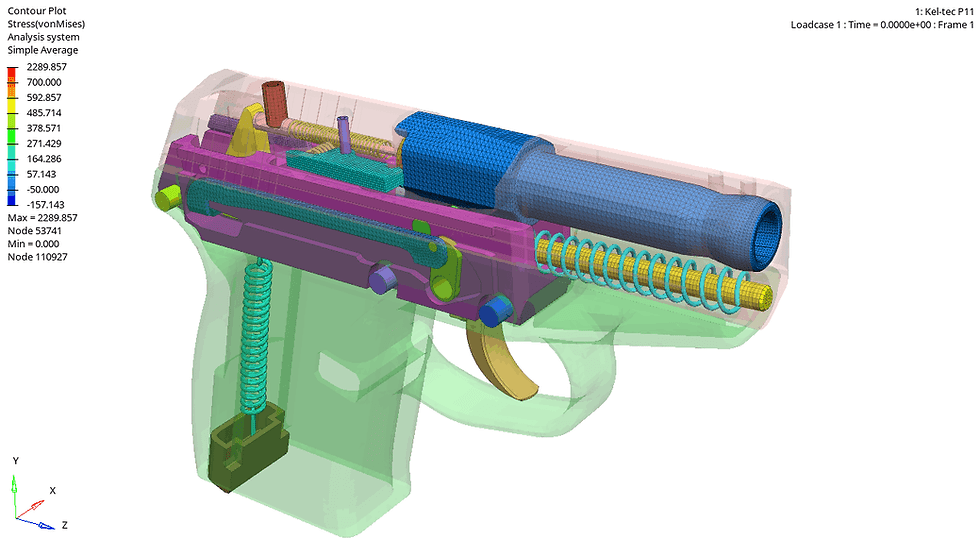
An Internal ballistics simulation using Fluid Structure Interaction (FSI) method
The aim of this simulation was to show the capabilities of the FSI approach for solving the dynamic behavior of Kaltec P11 pistol.
Gun powder is simulated with Smoothed Particle Hydrodynamics (SPH) Elements [2],[3]
The motivation behind the use of SPH particles in these kind of simulation, is, the fact that they capable of extremely large deformations, which is more complicated in traditional FSI simulation when a CFD solver Coupled with structural explicit solver.
Gun powder is modeled with Jones Wilkins Lee Equation of State, JWL - EOS [4]. this equation of state is often used to simulate explosives.
All parts, including springs are modeled with FEA explicit method, that means - all parts show the strains stresses and other mechanical outputs.
springs are pre-tensioned in a different simulation, and strain and stresses of the pre-tensioned springs added to the complete model.
[2] https://en.wikipedia.org/wiki/Smoothed-particle_hydrodynamics
[3] Randles P.W. and Libersky L.D., “Smoothed Particle Hydrodynamics: Some recent improvements and applications”, Computer Methods Appl. Mech. Engrg. Vol. 139, pp. 375-408, 1996.
Arkal Automotive

Battery Tray crash
Simulation of a front vehicle chassis, assembled with an Arkal-Automotive battery tray.
Aim was to check battery tray capability of withstanding a car frontal crash at 56 km/h, check and compare material behaviour and part behaviour to real life testing.
In this simulation the maximum acceleration reached a peak of 50g.
*The above video is the propety of Arkal- Automotive, and more info and simulations can be found on their page -
https://www.arkal-automotive.com/product-design
Bullet hits soda can



Fluid Structure interaction with 9mm bullet hits a soda can
The purpose of this simulation is to simulate high velocity impact using an explicit solver.
The simulation introducing an XFEM ( eXtended Finite Element Method) crack propagation and element failure technique (ALTAIR - Radioss)
Further, the water in this simulation is modeled with the use of SPH [3] elements.
Finnaly a render of the simulation is done with the use of SolidThinking - Evole.
Helmet test




Soft material Helmet - ground hit
This simulation is a part of Development process of a soft material helmet.
The aim of the simulation is to check if there are catastrophic failures in the helmet materials and can the helmet withstand a ground hit without peaking acceleration of 300[g].
The simulation Boundary conditions were configured based on the CPSC standard for helmet testing -
https://www.cpsc.gov/Business--Manufacturing/Business-Education/Business-Guidance/Bicycle-Helmets
The helmet material is hyper elastic, modeled with Ogden material law [5],
Ogden material law in short, describes the behavior of in-compressible (Poisson's ratio ~ 0.5) hyper elastic materials, capable of high deformations (strains of 600%).
In contrast to the classical solid mechanics, where the small displacement theory is used, when dealing with highly deformable materials the use of non linear solid mechanics must take place [6] [7]
[5] https://en.wikipedia.org/wiki/Ogden_(hyperelastic_model)
[6] Bonet, J., and R. D. Wood. "Nonlinear Solid Mechanics: A Continuum Ap-proach for Engieeering." (1997). chapter 6
[7] https://en.wikipedia.org/wiki/Deformation_(mechanics)